Pneumatic double diaphragm pumps in the ceramic industry
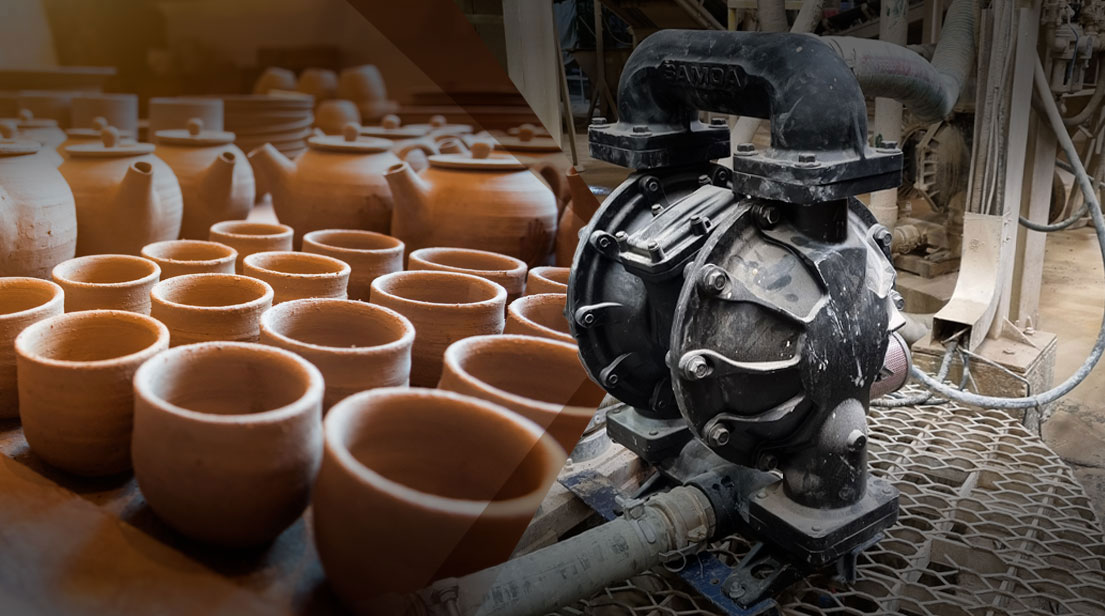
Pneumatic double diaphragm pumps in the ceramic industry
If you work in the ceramics industry and need guidance on choosing the right pumping solution, this article will provide valuable insights.
Ceramic production involves unique challenges, making the selection of an appropriate pump a complex decision. Transferring fluids such as slip, ceramic glazes, and wastewater is an essential part of the process. These applications require durable and adaptable pumps that can handle fluids with suspended solids.
For any fluid handling needs within the ceramic industry, SAMOA recommends air-operated diaphragm pumps.
This guide covers:
How air-operated diaphragm pumps function and why they are advantageous compared to other options.
The key applications of these pumps in ceramic production and the most suitable models for each.
An example installation to illustrate their use in real-world settings.
How Air-Operated Diaphragm Pumps Work and Why They Are Ideal for Ceramics
Pneumatic diaphragm pumps offer several key benefits for ceramic manufacturing:
• Adjustable flow rates, with capacities up to 1,000 l/min (264 US gal/min).
• Ability to handle suspended solids without affecting fluid temperature.
• High resistance to abrasive materials, which are common in ceramic processes.
• Lower energy consumption compared to electric pumps.
• Extended lifespan, leading to reduced maintenance costs.
• Simplified servicing, as fewer components result in shorter downtimes.
• Secure bolted construction, minimizing leakage risks and simplifying maintenance with uniform bolt sizes.
• ATEX certification availability, ensuring safe operation in hazardous environments.
Applications and recommended Pump Models
1. Ceramic Glaze and Color Preparation
Ceramic glazes consist of inorganic frits in granulated or flake form, mixed with water to create the final formulation. These are applied to products such as porcelain, tiles, and stoneware.
Recommended pump: 2″ metallic air-operated diaphragm pump with Hytrel or Santoprene diaphragms
Hytrel diaphragms offer excellent resistance to abrasion.
Santoprene diaphragms provide flexibility for handling suspended solids.
2. Dispensing and Color Mixing
Air-operated diaphragm pumps are widely used in ceramic color kitchens and dosing systems.
Recommended pump: 1″ air-operated diaphragm pump
• Chosen for its suitability in low-flow applications.
• Material selection should align with the specific fluid properties.
3. Ceramic Glaze Spraying
These pumps are frequently used in spraying applications for ceramic glazes.
Recommended pumps: ½″ or 1″ air-operated diaphragm pumps
• For solvent-based glazes → Aluminum pump with Teflon diaphragms.
• For water-based glazes → Aluminum pump with Santoprene diaphragms.
4. Tile Printing
Tile printing systems transfer ceramic colors from storage tanks to printing rollers, which apply the design onto the tiles.
Recommended pump: 1″ air-operated diaphragm pump
• Ensures smooth and accurate color transfer from 20-40 liter tanks.
5. Ceramic Slip and Paste Transfer
Pneumatic diaphragm pumps are well-suited for transporting ceramic slip (barbotine) and pastes in production lines.
Recommended pump: 3″ metallic air-operated diaphragm pump with Hytrel or Santoprene diaphragms
Designed to handle high flow rates and abrasive materials.
6. Wastewater Treatment in Ceramic Facilities
Before disposal, wastewater from ceramic production must be treated to meet environmental standards.
Recommended pump: 2″ aluminum air-operated diaphragm pump with Hytrel or Santoprene diaphragms
These materials provide strong resistance to suspended solids and maintain flexibility.
Teflon diaphragms are not advised, as their rigidity increases the risk of deformation and leakage.
Installation example
To illustrate the role of pneumatic diaphragm pumps in ceramic production, the following example outlines a real-world installation:
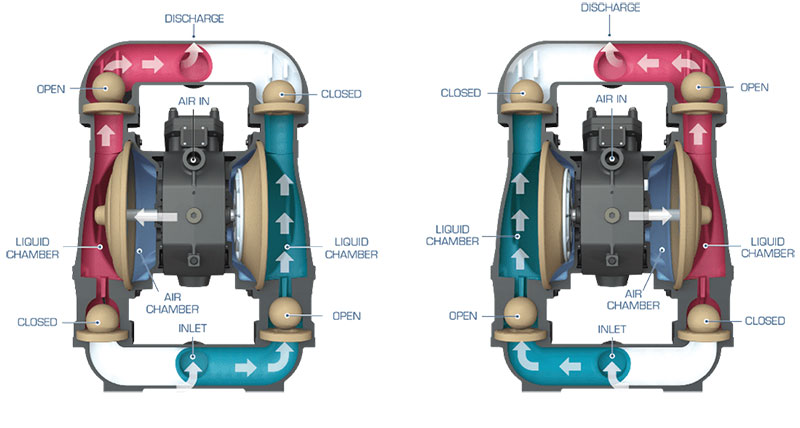
Applications and Recommended Pumps
1. Preparation and Mixing of ceramic glazes and colors
Ceramic glazes contain inorganic frits in granulated or flake form, which are mixed with water before being applied to porcelain, tiles, and stoneware.
Recommended pump: 2″ metallic air-operated diaphragm pump with Hytrel or Santoprene diaphragm
• Hytrel diaphragms offer excellent abrasion resistance.
• Santoprene diaphragms provide high flexibility for handling suspended particles.
2. Dispensing and color mixing
Air-operated diaphragm pumps are commonly used in ceramic color kitchens and dosing systems.
Recommended pump: 1″ air-operated diaphragm pump
• Ideal for low-flow applications.
• The pump material should be selected based on the specific fluid properties.
3. Spraying of ceramic glazes
These pumps are used for spray application of ceramic glazes.
Recommended pumps: ½″ or 1″ air-operated diaphragm pump
• For solvent-based glazes → Aluminum pump with Teflon diaphragm.
• For water-based glazes → Aluminum pump with Santoprene diaphragm.
Ceramic glazes contain inorganic frits in granulated or flake form, which are mixed with water before being applied to porcelain, tiles, and stoneware.
Recommended pump: 2″ metallic air-operated diaphragm pump with Hytrel or Santoprene diaphragm
• Hytrel diaphragms offer excellent abrasion resistance.
• Santoprene diaphragms provide high flexibility for handling suspended particles.
2. Dispensing and color mixing
Air-operated diaphragm pumps are commonly used in ceramic color kitchens and dosing systems.
Recommended pump: 1″ air-operated diaphragm pump
• Ideal for low-flow applications.
• The pump material should be selected based on the specific fluid properties.
3. Spraying of ceramic glazes
These pumps are used for spray application of ceramic glazes.
Recommended pumps: ½″ or 1″ air-operated diaphragm pump
• For solvent-based glazes → Aluminum pump with Teflon diaphragm.
• For water-based glazes → Aluminum pump with Santoprene diaphragm.
To illustrate how pneumatic diaphragm pumps are used in ceramic manufacturing, the following installation case is presented:
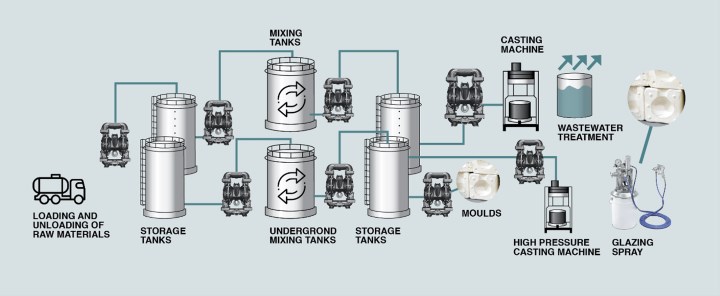
4. Tile Printing
Tile printing systems transfer ceramic colors from storage tanks to printing rollers, which apply the design onto the tiles.
Recommended pump: 1″ air-operated diaphragm pump
• Ensures smooth and precise color transfer from 20–40 liter tanks.
5. Transport of ceramic slip and pastes
• Pneumatic diaphragm pumps are used for transporting ceramic slip (barbotine) and pastes in production lines.
Recommended pump: 3″ metallic air-operated diaphragm pump with Hytrel or Santoprene diaphragm
• Designed to handle high flow rates and abrasive materials.
6. Wastewater treatment in ceramic facilities
Wastewater from ceramic production must be treated before discharge.
Recommended pump: 2″ aluminum air-operated diaphragm pump with Hytrel or Santoprene diaphragm
• Highly resistant to suspended particles and flexible in operation.
• Teflon diaphragms are not recommended, as their rigidity increases the risk of deformation and leakage.
Tile printing systems transfer ceramic colors from storage tanks to printing rollers, which apply the design onto the tiles.
Recommended pump: 1″ air-operated diaphragm pump
• Ensures smooth and precise color transfer from 20–40 liter tanks.
5. Transport of ceramic slip and pastes
• Pneumatic diaphragm pumps are used for transporting ceramic slip (barbotine) and pastes in production lines.
Recommended pump: 3″ metallic air-operated diaphragm pump with Hytrel or Santoprene diaphragm
• Designed to handle high flow rates and abrasive materials.
6. Wastewater treatment in ceramic facilities
Wastewater from ceramic production must be treated before discharge.
Recommended pump: 2″ aluminum air-operated diaphragm pump with Hytrel or Santoprene diaphragm
• Highly resistant to suspended particles and flexible in operation.
• Teflon diaphragms are not recommended, as their rigidity increases the risk of deformation and leakage.
By selecting the right air-operated diaphragm pump for each stage of production, ceramic manufacturers can improve efficiency, reduce maintenance downtime and ensure reliable fluid handling.