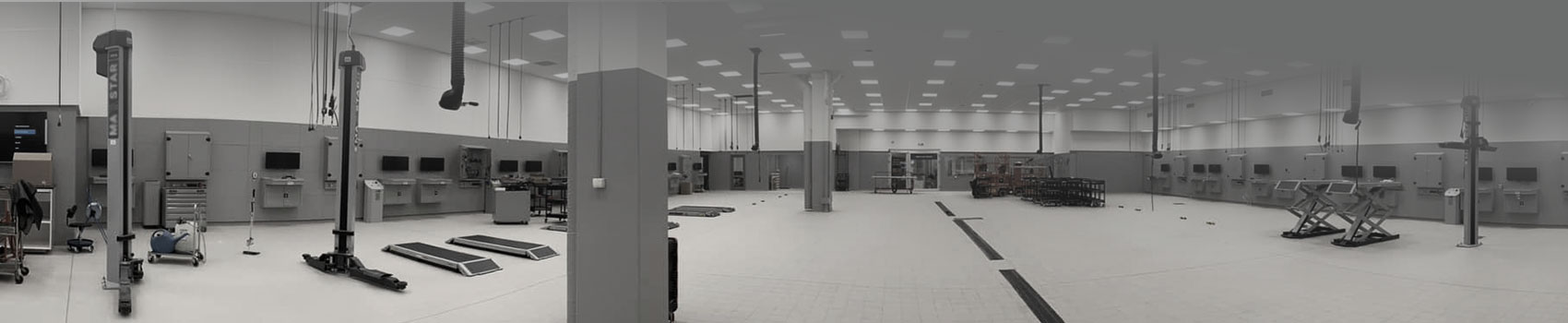
Case Study: Solving Challenges with SAMOA Solutions at Carlfors Bruk AB
Background
Carlfors Bruk AB, a global leader in the production of aluminum pigments and flakes, faced a significant operational challenge. Their production process involves handling aluminum powder and flakes mixed with naphtha—an abrasive, demanding fluid that requires highly durable and efficient pumping systems. The company needed a solution to improve pump performance, reduce operational costs, and ensure reliability in their manufacturing environment.
Challenge
The production process at Carlfors Bruk necessitated pumps that could:
• Efficiently handle abrasive fluids like aluminum powder and flakes in naphtha.
• Endure high levels of abrasion, temperature extremes, and operational fatigue.
• Operate with reduced energy consumption to minimize production costs.
• Maintain cost-effectiveness without sacrificing performance or durability.
The pumps previously in use struggled to meet these demands, leading to increased maintenance costs, energy inefficiency, and higher operational expenses.
Solution Provided by OrionFlow
OrionFlow collaborated with Carlfors Bruk AB to implement a tailored solution: the SAMOA UP20 Double Diaphragm Pump. This 2" pneumatic double diaphragm pump - part of the SAMOA Universal Pivot series - was selected for its ability to handle challenging production conditions effectively.
Key features of the solution include:
• Material Optimization:The pump utilizes Hytrel seats, balls, and diaphragms, which provided excellent durability and resistance to abrasion at a lower cost compared to the previously used PTFE components.
• Efficiency Gains: The UP20 pump demonstrated 40% lower air consumption compared to competing models, significantly reducing energy costs.
• Robust Design:The pump's aluminum wetted parts and optimized check-valves and manifolds ensure durability and reliable performance under abrasive and extreme conditions.
Implementation
OrionFlow guided Carlfors Bruk through the process of integrating the UP20 pump into their production line. Our team ensured seamless installation and provided training for maintenance staff to maximize the pump's operational life and efficiency.
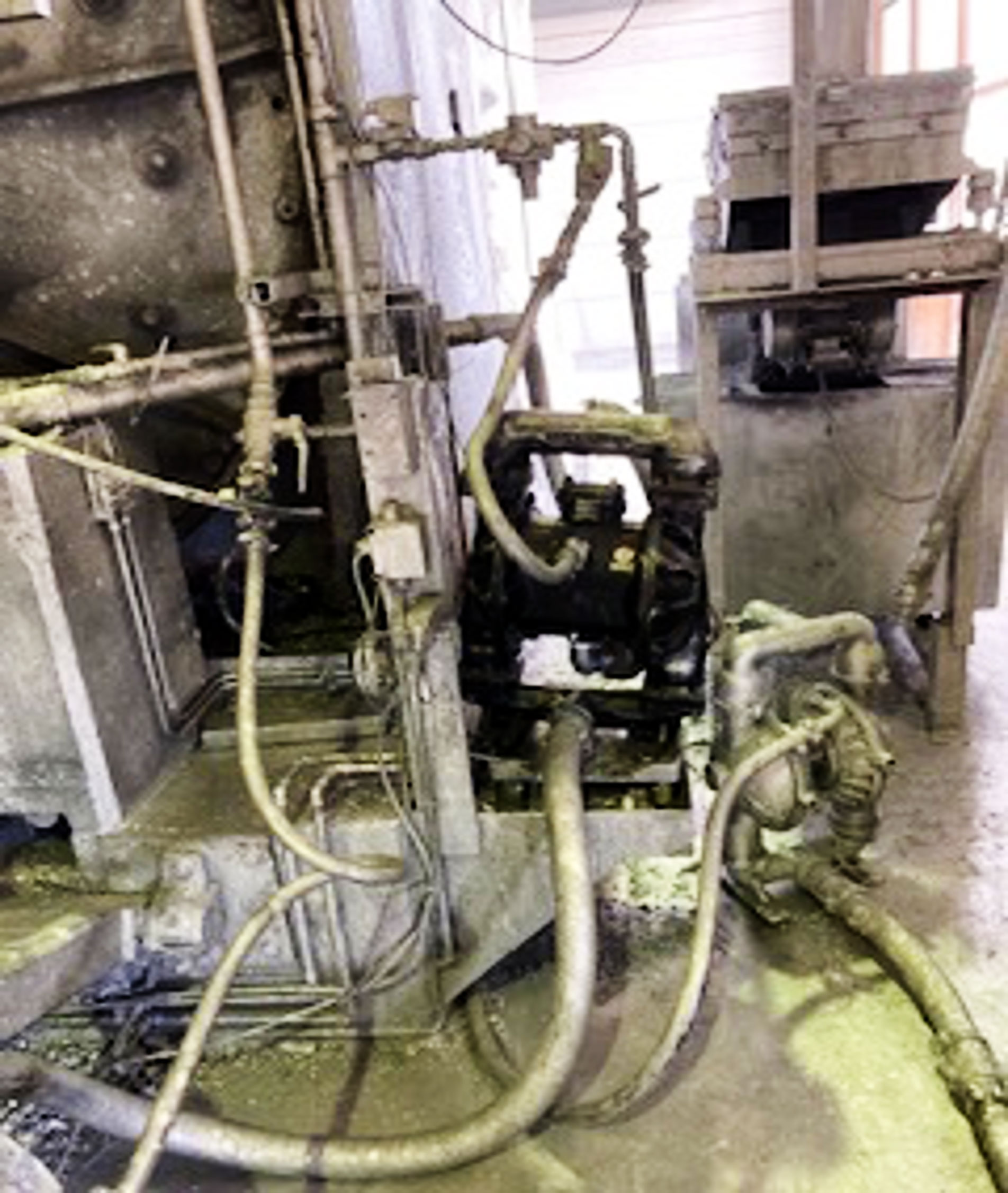
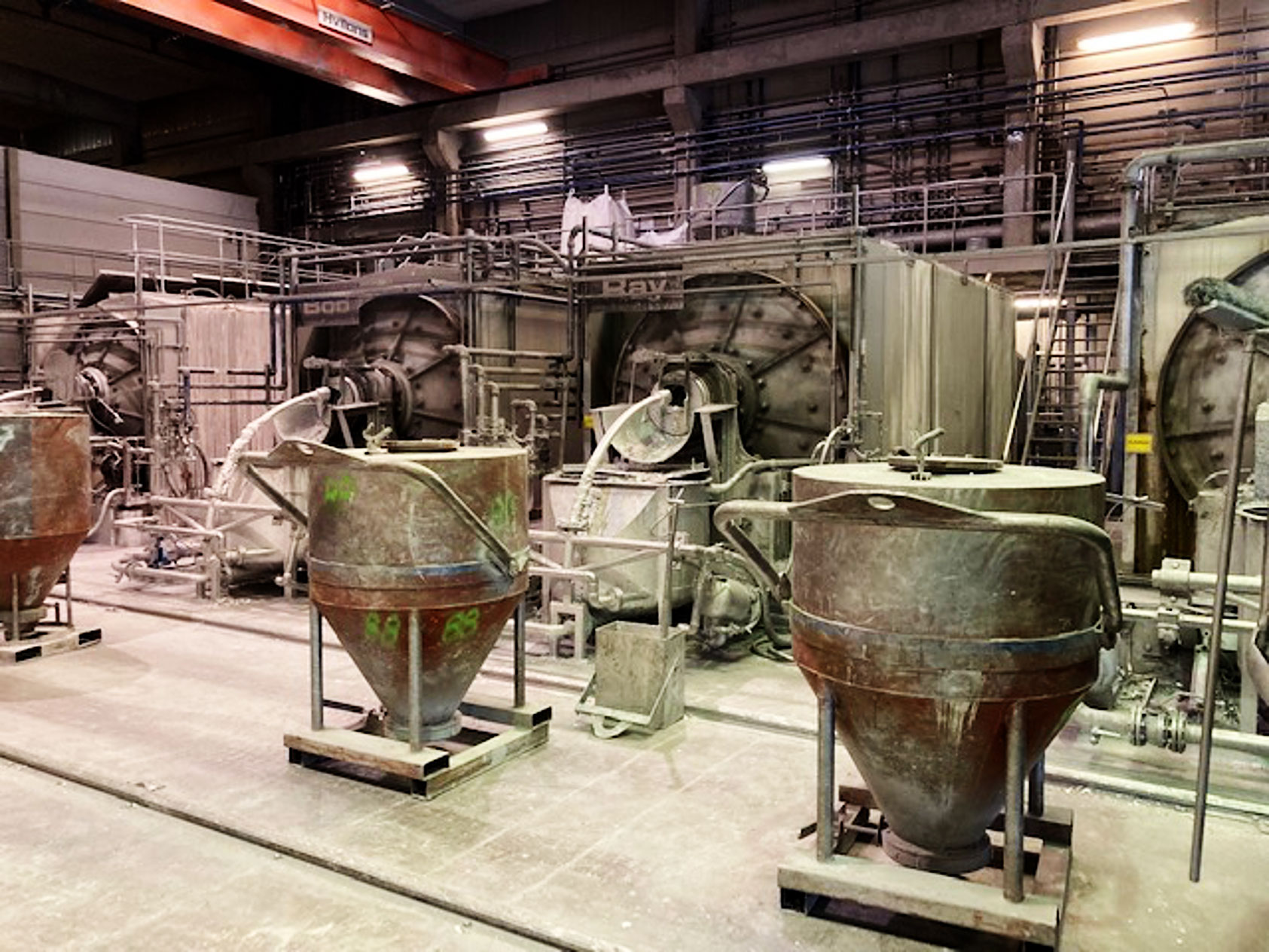
Results
The implementation of the SAMOA UP20 pump delivered immediate and measurable benefits:
• Reduced energy costs: With 40% lower air consumption, Carlfors Bruk achieved significant energy savings.
• Improved cost efficiency: The switch to Hytrel materials drastically reduced component costs without compromising performance.
• Enhanced reliability: The pump's durability and optimized design minimized downtime and maintenance needs, improving overall production efficiency.
• Customer satisfaction: According to Nicolas Regel, Maintenance Responsible at Carlfors Bruk AB, the UP20 pump "uses about 40% less air than the competitor’s pump," highlighting the value of the solution provided by OrionFlow.
Conclusion
Through our partnership with Carlfors Bruk AB, OrionFlow demonstrated our commitment to delivering practical, high-performance solutions tailored to our customers’ unique challenges. By implementing the SAMOA UP20 Double Diaphragm Pump we helped Carlfors Bruk optimize their operations, reduce costs, and improve production reliability, underscoring the effectiveness of OrionFlow’s solutions in demanding industrial environments.
For more details or inquiries, please contact:
Svante Fogelhamre
Business Area Manager Flow
+46 (0)76 163 01 79
svante.fogelhamre@alentec.se